DISCOVER THE AMAZING PERKS OF ULTRASONIC PARTIAL DISCHARGE DETECTION
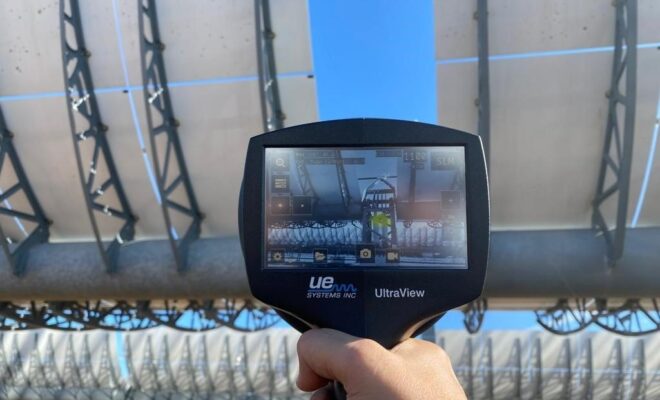
Contemporary society depends on electrical infrastructure because it distributes power to production facilities, urban zones, and critical installations that serve the population. However, electrical assets undergo deterioration from age and environmental stress, which makes them vulnerable to partial discharge (PD) events that harm insulation materials and cause equipment failure incidents.
The detection of PD at an early stage is essential for operational reliability and ultrasonic detectors have become key instruments for this purpose. These devices detect PD before it escalates into major problems, thus enabling maintenance staff to stop equipment breakdowns, minimize operational interruptions, and improve safety measures.
This article evaluates the multiple advantages of using a partial discharge ultrasonic detector.
What distinguishes a partial discharge ultrasonic detector as an instrument?
A partial discharge ultrasonic detector is an assessment tool that identifies high-frequency sound waves from electrical discharges. The frequencies of PD exceed human hearing thresholds (above 20 kHz) but ultrasonic detectors use sound translation to provide audible and visible results for engineering analysis.
The main advantage of ultrasonic detectors over traditional methods is their portable nature and intuitive operation for detecting partial discharges inside and outside buildings effortlessly.
The key advantages of using ultrasonic PD detection
It identifies partial discharges ahead of time
An ultrasonic PD detector identifies partial discharge at its initial stages. An early PD detection allows operation teams to assess equipment before a small problem transforms into a critical system failure due to deteriorating insulation.
The identification of PD issues in their initial phases allows utilities and industries to prevent these outcomes:
- Costly transformer and switchgear failures
- Unexpected power outages
- Dangerous electrical fires
Non-intrusive and safe inspection
Ultrasonic detectors enable safe non-intrusive inspections by eliminating the need to handle high-voltage equipment. Maintenance personnel can check electrical parts from a remote distance, thus minimizing their contact with dangerous hazards.
This is especially valuable in:
- Substations that operate at high voltage levels, posing the danger of direct contact.
- The inspection of limited-access spaces.
- Maintenance situations involving active electrical systems that cannot be de-energized for inspection.
The equipment determines the exact position of PD events
Besides detecting PD, ultrasonic detectors show exactly where breakdown occurs. Sound intensity scans from technicians give them the ability to detect particular PD locations within the transformer, cables, switchgear, or insulators.
The accurate results produced by ultrasonic detectors remove the need for guessing so maintenance organizations can make precise interventions instead of wasting money on complete system replacement.
Works in noisy environments
The detection of partial discharge (PD) becomes difficult when technicians work in environments with substantial background noises such as substations and industrial facilities with their heavy machinery operating. Ultrasonic detectors use a purpose-built noise filtering system which tracks only the high-frequency sounds that come from PD.
The detection system works effectively in noisy surroundings, which makes it better than other standard detection methods that may fail to work in such environments.
Portable and easy to use
The past has marked the end of handling complex bulky equipment for PD detection. Modern ultrasonic detectors are:
- Compact and lightweight, allowing for easy transportation.
- Easy to operate without specific training demands.
- Quick to deploy, which enhances inspection velocity while improving decision-making processes.
Ultrasonic PD detectors work effectively because of their portable design and quick deployment features, which benefit maintenance teams seeking mobile and fast solutions.
Reduces maintenance costs
Preventive maintenance initiative proves less expensive than performing urgent repairs. Testing for PD early with ultrasonic detectors ensures that insulation breakdowns stay ahead of time and prevent the following sequence of events:
- Expensive equipment replacements.
- Emergency repair costs.
- Downtime-related financial losses.
The implementation of ultrasonic detection systems lets organizations move away from basic maintenance practices to proactive prediction techniques. This creates durable financial and operational benefits.
Extends power system reliability
PD detection failures result in excessive electrical equipment deterioration and system breakdowns, leading to power outages. Regular maintenance programs benefit from ultrasonic PD detection implementation through these advantages:
- Ultrasonic detection extends the operational life of electrical equipment components.
- Proper early detection of problems reduces power failures in electrical systems.
- A maintained power supply offers reliability to customers and operational stability
All businesses, utilities, and essential service operations need a dependable power supply for uninterrupted performance. Ultrasonic detection systems maintain operational integrity and performance of electrical systems.
Environmentally friendly maintenance approach
Ultrasonic PD detectors for preventive maintenance follow sustainability goals by minimizing three external effects:
- Unnecessary waste from damaged electrical components
- The loss of excessive amounts of energy due to inefficient electrical operation
- The environmental impact of emergency repairs and replacements
Businesses that perform proactive maintenance on their electrical assets help create sustainable power systems as well as energy-efficient technologies for the future.
It can identify different forms of limited discharge inside electrical equipment
Partial discharge exists as three different forms, which include:
- Corona discharge caused by high voltage stress
- Surface discharge (along the surface of insulating materials)
- Internal discharge (inside insulation defects)
Ultrasonic detectors recognize and identify all three types of discharge, thus providing complete inspection capabilities for electric power systems maintenance.
Can function with other maintenance technology systems
The combination of Ultrasonic PD detectors functions effectively with other electrical assessments.
- Thermal cameras detect excessive heat generation caused by PD occurrences.
- Acoustic imaging technology uses advanced detectors to create images of PD emissions.
- Electrical tests evaluate insulation resistance together with system performance through their analysis.
These interconnected technologies help maintenance groups build inclusive asset-monitoring systems to ensure optimal asset reliability.
The key takeaways
Partial discharge functions without noticeable signs until it causes severe equipment breakdowns, power interruptions, and safety issues. The right diagnostic instruments allow for early partial discharge identification, which prevents excessive cost burdens.
The implementation of partial discharge ultrasonic detectors brings multiple advantages to users through:
- Identifying issues early enough to stop deterioration from worsening.
- Detecting PD with ease through its non-intrusive and secure operation design.
- Giving accurate and precise identification of where faults exist.
- Cost savings through predictive maintenance.
- Enhanced power reliability and asset lifespan.
Utility operators, industrial facilities and facility management departments should adopt ultrasonic PD detection as a strategic investment because it protects their electrical infrastructure while guaranteeing continuous operations. Ultrasonic detection of partial discharge allows organizations to decrease their risks and expenses while preserving their power system reliability.